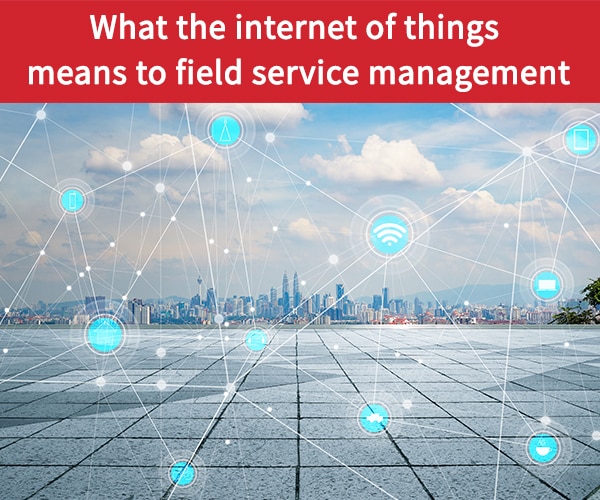
- Field Service Management
- Internet of Things
- Maintenance
What the Internet of Things means for Field Service Management.
As technology continues to advance, we hear more and more about the Internet of Things (IoT). But, it’s often not clear how the evolution to IoT technology will affect all of the different people and processes associated with field service management.
The good news is that IoT will bring immediate benefits to the industry and its customers. Field service companies will be in a far better position to streamline service management and improve customer service. Service technicians will no longer visit customers to fix equipment failures, but to ensure those failures don’t occur. And, in the eyes of customers, this fact will make all the difference.
Let’s explore the potential for IoT in field service management, starting with what exactly it is.
A network of connected objects
The IoT connects any object with a sensor to the Internet so that object can communicate. The connected object could be anything from a dishwasher to a car, a smartphone, even clothing.
The National Basketball Association (NBA) is already using connected clothing to strengthen the relationship between players and fans. Sports equipment manufacturer, Nike, embedded sensors into players’ jerseys so fans can track the performance of their favorite player, find stores that sell items featuring the player’s name, and receive special offers on ticket prices.
Basically, anything that can transmit data over a wireless network can become part of the Internet of Things.
IoT field service : New connections bring new opportunities
The advent of IoT technology opens the door to a vast array of possibilities in the field service management industry. Field service providers will be able to connect vehicles, customer equipment and machines to the Internet so they can communicate with them to remotely control their operation and retrieve data about wear rates.
Ultimately, they will be able to solve customers’ problems faster.
IoT and Technicians
The Internet of Things (IoT) is revolutionizing the work of field service technicians in transformative ways. The deployment of IoT devices in various sectors, such as manufacturing, telecom, and healthcare, is paving the way for real-time monitoring of equipment, leading to predictive maintenance capabilities. This means technicians can now be alerted about potential equipment failures before they occur, allowing for proactive maintenance and significantly reducing downtime.
Moreover, IoT enhances remote diagnostics, enabling technicians to identify and solve issues without even needing to be physically present at the site. This not only saves travel time and costs, but it also boosts productivity. Additionally, the use of IoT is enriching data collection and analysis, giving field service technicians unprecedented access to detailed data to make well-informed decisions, improve service delivery, and ultimately increase customer satisfaction. Indeed, IoT’s impact on field service is truly transformative and positions the sector to be more efficient, effective, and customer-centric.
OPTIMIZE OPERATING TIME FOR EQUIPMENT
With connected equipment and specialized software, field service companies will be able to analyze the data sent by sensors in real time so they can replace parts just before a failure occurs. By anticipating and avoiding equipment failures, service companies can help their customers optimize the amount of time equipment can be used.
EVOLVE TOWARD PREDICTIVE MAINTENANCE
Field service companies can also use IoT technology to evolve from corrective, or curative, maintenance to predictive maintenance. Now, customers enjoy a far better service experience. Maintenance occurs before problems can arise. And customers don’t have to deal with the more serious damage that can occur as a result of the domino effect that can a single failure can cause.
Implementing IoT
There are many different ways to bring IoT technology into the heart of field service management.
INSTALL SENSORS ON EQUIPMENT
The first step is to install communications-enabled sensors on equipment at customer sites. Sensors are available to monitor pressure, temperature, humidity and other levels on equipment that requires regular monitoring for maintenance purposes. The sensors allow equipment to communicate operational information to a database, a service technician, or a service center.
The information sent by sensors allows you to anticipate failures rather than being forced to react to emergencies after equipment has failed. The ability to anticipate and avoid failures is particularly important in industries where the ability to avoid stopping a production line due to an equipment breakdown can also save the customer a significant amount of money.
CONNECT TECHNICIANS’ VEHICLES
To deliver the best possible customer service, technicians must be efficient while working on-site and while on-the-move between customer sites. Adding sensors to technicians’ vehicles helps field service companies quickly assess whether travel times are good, or whether lengthy journeys are reducing productivity.
They can also use the technology to identify the fastest route to get to a customer site and to optimize technicians’ travel routes.
Our similar articles.
-
- Field Service Management
- Field Service Software
- scheduling software
Pitfalls of Using Free Field Service Management Software
September 4, 2024 -
- Technician
- Maintenance
- Gestion d’interventions
- Security
- Application mobile
- Technicien
Ensuring the safety of maintenance technicians
November 25, 2020 -
- Field Service Management
- Mobile App
- Predictive Maintenance
Top 3 field service trends to look out for in 2023
January 13, 2022